Custo de estoque: quais são e como calcular?
Fazer um bom gerenciamento de estoque é essencial para qualquer empresa. Sem compreender os custos associados a ele, dificilmente será possível tomar boas decisões e gerenciar o projeto de maneira eficiente. Sendo assim, entender o custo de estoque costuma ser o primeiro passo para otimizar o empreendimento a partir de um setor tão importante.
É por isso que, neste artigo, discutiremos os diferentes tipos de custos de estoque e mostraremos como calculá-los para ajudar você a otimizar seu gerenciamento de estoque e maximizar seus lucros. Confira.
O que é o custo de estoque e qual a importância?
Quando falamos em custo de estoque estamos nos referindo à soma dos variados gastos referentes à armazenagem de itens que permitem o funcionamento do negócio. Assim, precisam ser considerados elementos como:
- o aluguel;
- a energia elétrica;
- a depreciação dos equipamentos;
- os impostos;
- os contratos de segurança;
- os seguros;
- tudo que serve para acondicionar as mercadorias;
- a remuneração e os benefícios dos profissionais.
Logo, trata-se de um levantamento de informações que de modo algum deixa de ser complexo. Por isso, faz todo o sentido calcular o custo do estoque. Ele é importante para que a empresa tenha o devido controle sobre suas despesas operacionais.
Mais do que isso: o custo do estoque, quando devidamente assimilado, torna-se útil em relação às margens e o lucro líquido do negócio.
Na prática, o custo de estoque é ferramenta importante para ajudar na margem de lucro de uma empresa, permitindo que ela tenha uma melhor organização do ponto de vista financeiro. Não por acaso, a redução desses custos acaba sendo uma das metas principais da gestão de estoque.
A dificuldade de calcular o custo de estoque
A questão é que, justamente por se tratar de uma tarefa que envolve uma série de elementos, o cálculo do custo de estoque costuma ser difícil. Entre as dificuldades que mais comprometem a ação das empresas está saber qual é a quantidade exata de ativos que precisam ser armazenados, além do tempo ideal para tanto.
Em casos em que a empresa tem em estoque uma quantidade maior do que o necessário, ela fica sujeita a riscos como o de perder dinheiro com o armazenamento e também com a manutenção.
Da mesma forma, se ela estocar um número inferior do que o necessário, uma consequência negativa pode ser a falta do produto exatamente quando mais se precisa dele, ou seja, na hora que o cliente faz o pedido.
Pior ainda quando não existe o cálculo do custo do armazenamento por produto. Aluguel de espaço, energia elétrica, seguro, limpeza, entre outros, precisam ser devidamente registrados e mensurados.
Portanto, é importante saber quais são os custos e como mensurar exatamente quanto determinado ativo realmente custa para a empresa.
Quais são os tipos de custo de estoque
Custo de pedido
O custo de pedido é um elemento importante no gerenciamento de estoque empresarial. Ele se refere aos custos associados à realização de um pedido para reabastecer o estoque. Isso inclui dois elementos, de maneira geral:
- o custo do tempo e do trabalho necessário para preparar e enviar o pedido;
- as taxas ou despesas relacionadas ao processamento do pedido.
São exemplos os custos associados à preparação da documentação necessária para o pedido, como faturas e formulários de pedido. Da mesma forma, podem ser considerados os custos relacionados ao transporte e entrega dos itens solicitados.
Também é importante levar em consideração quaisquer taxas ou despesas cobradas pelo fornecedor para processar o pedido.
Custo de manutenção e armazenamento
O custo de manutenção e armazenamento se refere aos custos associados ao armazenamento do estoque. Isso inclui:
- o aluguel do espaço de armazenamento;
- os custos de energia e utilidades;
- os salários dos funcionários responsáveis pelo gerenciamento do estoque;
- quaisquer outras despesas relacionadas à manutenção do estoque.
São custos relacionados à manutenção do espaço de armazenamento, procedimentos como limpeza e reparos. Além disso, podem ser citados o uso de sistemas de gerenciamento de estoque e a contratação de funcionários para gerenciar o estoque.
Também é importante levar em consideração quaisquer despesas relacionadas à segurança do estoque. É o caso da instalação de sistemas de segurança e da contratação de seguranças.
Custo de produto
O custo do produto tem a ver com os custos associados à compra dos produtos que compõem o estoque. Assim, é preciso pensar não somente no preço pago pelos produtos, mas também em quaisquer impostos ou taxas relacionadas a essa compra.
Para ficar mais claro: é o caso de impostos que incidem sobre vendas ou sobre a importação de um produto. Além disso, pode haver taxas de corretagem ou taxas de câmbio que precisam ser levadas em consideração ao calcular o custo total do produto.
Custo de falta de estoque ou excesso
O ideal é gerenciar o estoque com equilíbrio, de maneira que não falte ou sobre estoque. Entretanto, o custo de falta de estoque ou excesso costuma aparecer quando a empresa tem pouco ou muito estoque. Isso porque, quando se tem pouco estoque, a consequência geralmente é a perda de vendas e insatisfação do cliente.
Por outro lado, quando se tem estoque demais, a tendência é que isso resulte em desperdício e obsolescência.
Uma empresa que não tiver estoque suficiente para atender à demanda dos clientes, certamente pode perder vendas e receita. Pior ainda: seus clientes podem ficar insatisfeitos e procurar outras empresas para atender às suas necessidades.
Por outro lado, se uma empresa tiver estoque em excesso, ela pode ver seus itens não serem vendidos. Isso gera obsolescência. Como consequência, é possível que essa empresa tenha que conviver com desperdício e até a perda financeira.
Custo de depreciação ou custo de risco
O custo de depreciação ou custo de risco é o custo associado à perda de valor dos produtos em estoque ao longo do tempo. Isso pode ser causado por diferentes fatores. Entre os principais estão:
- obsolescência;
- deterioração e;
- danos.
Imagine uma empresa que trabalha com produtos eletrônicos, por exemplo. Neste cenário, é fato que eles podem se tornar obsoletos rapidamente. Especialmente na medida que novas tecnologias são lançadas. Se isso acontecer, a consequência será uma perda de valor para os produtos em estoque.
Além disso, produtos perecíveis podem se deteriorar ao longo do tempo, resultando em perda de valor. Também é importante levar em consideração quaisquer danos que possam ocorrer aos produtos em estoque, como danos causados por transporte ou manuseio inadequado.
Ao gerenciar esse tipo de estoque é importante levar em consideração o custo de depreciação ou custo de risco e tomar medidas para minimizá-lo. É o caso da rotação regular do estoque para evitar a obsolescência e a deterioração, bem como a implementação de medidas para evitar danos aos produtos em estoque.
Custo de serviço
O custo do serviço está associado ao fornecimento de serviços aos clientes relacionados ao estoque. Isso pode incluir coisas como:
- suporte ao cliente;
- garantias e;
- devoluções.
No caso de uma empresa que oferece suporte ao cliente para seus produtos, por exemplo, ela certamente tem custos com a contratação de funcionários para fornecer esse suporte.
Além disso, se a empresa oferece garantias ou permite devoluções de produtos, ela também arca com custos associados ao processamento dessas garantias e devoluções.
Para lidar com esse tipo de custo é importante pensar na implementação de medidas para reduzir a necessidade de suporte ao cliente, como fornecer informações claras sobre os produtos e garantir que eles sejam de alta qualidade.
Também podem ser implementadas políticas claras de garantia e devolução para minimizar os custos associados a esses serviços.
Assuma o controle dos seus custos com a planilha de gestão de estoque! Acesse o material gratuitamente.
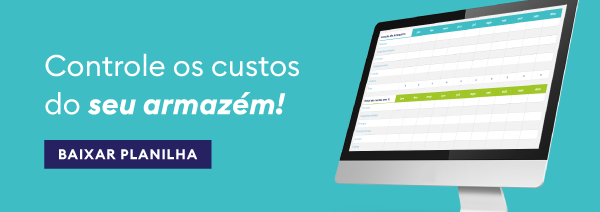
Como calcular o custo de estoque
A realidade é que o custo de estoque depende da realidade de cada empresa. Assim, é preciso considerar a atividade que ela realiza e o modelo de estoque com o qual trabalha.
Ainda assim, é bastante comum que o cálculo do custo de estoque seja resultado da soma de todos os custos associados a ele. Dessa forma, é preciso considerar os 7 elementos citados. No caso:
- custo de pedido;
- custo de manutenção e armazenamento;
- custo do produto;
- custo de falta de estoque ou excesso;
- custo de depreciação;
- custo de risco;
- custo do serviço.
Vamos exemplificar: imagine que uma empresa tem um custo de pedido no valor de 100 Reais por pedido.
Acrescente a isso, 200 Reais por mês com custo de manutenção e armazenamento, um custo do produto de 10 Reais por unidade, um custo de falta de estoque ou excesso de 500 Reais por mês, um custo de depreciação ou custo de risco de 20 Reais por mês e um custo do serviço de 30 Reais por mês.
Somando todos esses valores, chegamos ao custo total do estoque de 410 Reais por mês.
Como fazer os registros de custo de estoque?
É importante que os registros de custo de estoque se tornem uma prática regular por parte da empresa. O motivo é que somente assim será possível controlar esse tipo de despesa de maneira a evitar que ela saia de controle.
Para tanto, o ideal é considerar tanto as necessidades quanto as preferências da empresa. Algumas delas, especialmente as de pequeno porte, podem trabalhar com ferramentas simples. Para outras, que contam com estruturas mais complexas, o indicado é recorrer a sistemas mais sofisticados.
De qualquer forma, soluções que vão desde planilhas eletrônicas até softwares contábeis e sistemas de gerenciamento de estoque mais avançados são úteis para registrar e acompanhar os custos de estoque.
O importante é ter como registrar essas despesas, considerando os 7 tipos apresentados. Além disso, fazer a atualização dos registros de maneira regular. Assim é possível ter a garantia de que eles estarão sempre precisos e em dia com a realidade da organização.
Uma dica é categorizar e organizar os registros de maneira lógica. Isso será importante para simplificar a análise e a futura tomada de decisões. Nesse sentido, sistemas mais robustos são recomendados, uma vez que eles podem classificar os custos de maneira automática, considerando tipo ou período.
Assista ao video abaixo e confira o dia a dia do gestor de logística.
Como reduzir os custos de estoque?
No geral, a melhor maneira de lidar com custos excessivos no estoque é criando uma lógica em relação a esse setor tão importante do negócio.
Isso pode ser feito a partir de passos simples. É o que vamos mostrar como fazer agora.
Passo 1. Padronização
Procure padronizar e dotar de inteligência o gerenciamento do estoque da sua empresa. A melhor maneira de fazer isso é investindo.
Soluções tecnológicas e profissionais com capacidade estratégica podem representar um custo em um primeiro momento, mas converter isso em retorno em um segundo momento.
Passo 2. Controle
Tanto as entradas quanto as saídas do estoque devem ser acompanhadas em tempo real. Isso, além de dar agilidade ao negócio, permite também que desperdícios sejam evitados, algo que é essencial em relação ao estoque.
Passo 3. Curva ABC
É preciso saber quais são os itens que trazem o melhor resultado para a empresa. Dessa forma, ela tem como atuar na valorização destes e pensar em alternativas para os demais.
Passo 4. Reordenação
É importante que a empresa configure os chamados alertas de reordenação. Eles são notificações emitidas por software que avisam quando um item está chegando a um nível crítico no estoque.
Com eles é possível ter maior tranquilidade em relação à compra de itens sem que a empresa precise gastar mais do que o necessário.
Passo 5. Organização
É importante ter o controle sobre as mercadorias e o impacto que elas trazem para o empreendimento.
É a partir disso que será possível eliminar o excesso e trabalhar com uma estrutura mais enxuta e condizente com as necessidades do negócio.
Importância do giro de estoque
Por fim, vale citar também a importância do giro de estoque no controle desses custos. Ele nada mais é do que um indicador logístico que mostra a quantidade de vezes que o estoque é reposto em um determinado período de tempo.
Consequentemente, essa medida avalia se existe o equilíbrio entre as vendas realizadas e a compra de produtos.
O giro de estoque é importante porque ele nivela o estoque de produtos. Por meio desse cálculo é possível adequar o estoque à demanda. Da mesma forma, o giro permite diminuir custos com armazenagem e compreender melhor a rotatividade das mercadorias.
Agora que entendeu o que é custo de estoque e como calcular, confira também 3 dicas para resolver o problema de estoque parado.